1 ·概述
在传统的筒仓滑模施工过程中,遇到设有预埋件的环梁处时,通常的施工方法为筒仓滑至环梁下口结束,然后滑空、加固,进行支承环梁的施工,接着从支承环梁顶向上施工。筒仓预埋件环梁处施工工法通过环梁分两次浇筑,浇筑第一段时另一侧用泡沫板填充做模板,为保证其整体稳定性,筒仓滑至环梁底部约600 mm 时,在原有的滑模系统每个支撑杆间再加设一根48 钢架管,水平设两道拉杆,间距为600 mm,深入上部混凝土400 mm。在工程实践中,对施工工艺进行了认真探索总结,不断完善本工艺部分技术核心内容,填补国内相关空白。
2 ·工法特点
1) 筒仓预埋件环梁处施工工艺加快了施工进度、提高了工程质量,又具有十分良好的节能效果和综合经济效益。2) 本工艺避免了因等待环梁混凝土达到设计强度而造成的人员窝工,改善了工人作业的劳动条件,降低了劳动强度。3) 本工艺将原先环梁整体箍圈分成两部分,第一段浇筑混凝土,另一侧用泡沫板填充做模板,第二段浇筑环梁剩余部分来分段浇筑环梁,控制混凝土内部的水化热,混凝土内部振捣密实,保证混凝土施工质量。4) 本工艺通过滑模操作平台来施工环梁,不需要另外搭设操作平台,降低了施工难度,缩短了施工周期。
3· 适用范围
筒仓预埋件环梁处施工工艺可用于建筑工程中各类壁厚的筒仓、造粒塔等工业建筑,尤其适用于仓壁处设有预埋件的环梁构筑物。相关混凝土承载力、钢筋强度等一系列参数需经设计单位验算并符合规范同意后方可施工。
4· 工艺原理
筒仓预埋件环梁处施工工艺的原理是将原先环梁整体箍圈分成两部分,第一段混凝土浇筑壁厚度为150 mm,另一侧用泡沫板填充做模板,第二段混凝土浇筑为环梁的剩余部分( 见图1) 。
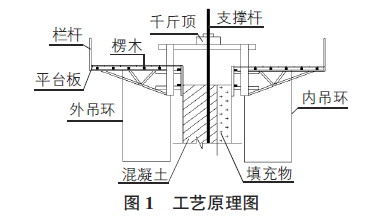
5· 施工工艺流程及操作要点
5. 1 施工工艺流程
支模、绑筋→先浇筑150 mm 壁厚混凝土( 另一侧用泡沫板填充做模板) →滑模系统滑至超出环梁顶400 mm 位置→绑扎环梁第二道箍圈→加设支撑杆( 48 钢架管) →预埋钢筋、钢板→浇筑环梁剩余部分混凝土。
5. 2 操作要点
滑模系统支撑完毕后,自基础环梁上标高开始滑模,滑升到漏斗环梁标高处利用滑模系统浇筑部分混凝土( 漏斗环梁为不规则的牛腿形状) ,剩余部分用竹胶板加钢架管支撑系统进行浇筑。
5. 2. 1 混凝土施工
1) 由于环梁分两次浇筑,为方便施工,经与设计沟通将原先整体箍圈分成两部分,第一段混凝土浇筑厚度为150 mm,第二段混凝土浇筑厚度为150 mm。2) 浇筑150 mm 壁厚混凝土时绑扎第一道箍圈,另一侧用泡沫板填充做模板,浇筑完毕后绑筋,绑扎第二道箍圈同时预埋钢筋和钢板,预埋钢筋和钢板焊接,最后整体浇筑剩余混凝土。3) 浇筑环梁另一侧混凝土时,应将先行浇筑的环梁内壁( 接槎面) 进行凿毛处理,一是将松散混凝土剔除,二是凿毛时最好形成坡口,这样易结合可提高整体强度。具体凿毛的标准按照4 cm × 3 cm 或5 cm × 4 cm( 水平尺寸与深度) 凿坑,四周间距10 cm ~ 15 cm,坑的密度越大,两次浇灌的接触面积也就越大,结合力也就越强。第二次浇灌时可加膨胀剂或采用高一标号的混凝土,混凝土施工图见图2。
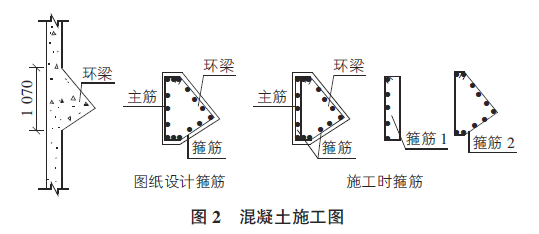
5. 2. 2 支撑系统加固
由于漏斗环梁处先分段浇筑150 mm 厚的筒壁混凝土,所以该处必须对支撑杆加固处理。具体加固方法为: 在原有的滑模系统支撑杆间再加设一根48 钢架管,深入下部混凝土600 mm,深入上部混凝土400 mm,为保证其整体稳定性,水平设两道拉杆,间距为600 mm。支撑杆示意图见图3。
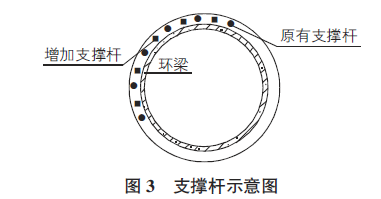
6·机械及设备投入计划
本工艺采用的机械或设备投入计划见表1。
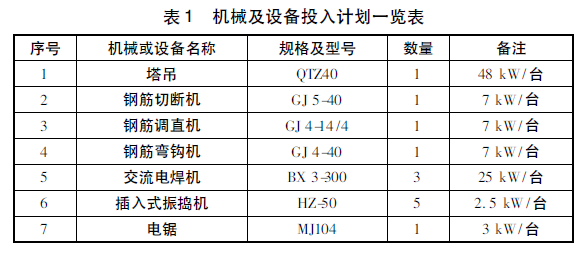
7· 质量控制
1) 工程质量控制措施。本工艺严格遵照施工技术规范和行业施工技术规程等进行施工和质量控制。2) 质量保证措施。预埋件和预留孔洞的施工方法: 采用直埋法,门、窗等洞口的胎模采用木模板和方木制作,宽度应小于滑升模板上口10 mm,并与仓壁钢筋固定牢靠。当达到预埋件埋设标高时,将预埋件与仓壁钢筋焊接,预埋件应与模板有一定间距,避免模板滑升时与模板接触,而产生挂模现象。
8 ·安全保证措施
1) 明确各人员安全生产责任制,认真贯彻执行“安全第一,预防为主”的方针。2) 作业人员严格执行国家相关法律法规,遵守现场安全管理制度。3) 班组进场前,进行入场安全“三级教育”,贯彻并签字。4) 班组作业前,编制有针对性的安全技术交底,向施工人员进行交底,并履行签字手续。5) 在构筑物仓壁边线外的10 m 范围内划为危险区域,此区内不得站人或通行。6) 构筑物出入口搭设高度不低于2. 5 m 的安全防护棚。安全通道棚顶采用不少于两层纵横交错的木板组成。7) 操作平台铺设的木架板必须严密平整、固定可靠并防滑,不得随意挪动。8) 操作平台设钢制防护栏杆,高度不小于1 200 mm,底部设高度大于180 mm 的挡板,栏杆外满挂安全网封闭。9) 操作平台上不用的材料、小型工具应及时清理运至地面。
9· 文明施工措施
1) 施工现场建筑垃圾按照指定地点堆放,做到施工完毕保持工完料尽,及时清理地面上的落地灰料。2) 泡沫板的堆放要整齐有序,做好防火措施,用塑料布进行覆盖,防止碎屑乱飞。3) 现场施工材料应分类堆放整齐并设置标识牌,分片包干到人。4) 尽量减少夜间施工,在施工时要采取减噪降噪的措施,将噪声控制在允许范围内。5) 做好现场防火工作,灭火设施配备齐全,设置专职消防员,定期进行安全隐患排查。6) 施工场地和道路经常洒水湿润,防止扬尘。
10· 结语
筒仓预埋件环梁处施工工艺与当前我国普遍使用的施工方法相比,有它的合理性、先进性及其适用性。采用前者施工工艺明显加快了施工进度、提高了工程质量,又具有十分良好的节能效果和综合经济效益,其效益可以概述为以下几点:
1) 施工操作简便,施工进度加快,施工质量提高,达到了预期的工期目标和质量目标。2) 施工所用工艺改善了作业条件,降低了劳动强度。3) 采用此工艺降低了工程造价,节约了施工成本,带来了良好的社会及经济效益。
在传统的筒仓滑模施工过程中,遇到设有预埋件的环梁处时,通常的施工方法为筒仓滑至环梁下口结束,然后滑空、加固,进行支承环梁的施工,接着从支承环梁顶向上施工。筒仓预埋件环梁处施工工法通过环梁分两次浇筑,浇筑第一段时另一侧用泡沫板填充做模板,为保证其整体稳定性,筒仓滑至环梁底部约600 mm 时,在原有的滑模系统每个支撑杆间再加设一根48 钢架管,水平设两道拉杆,间距为600 mm,深入上部混凝土400 mm。在工程实践中,对施工工艺进行了认真探索总结,不断完善本工艺部分技术核心内容,填补国内相关空白。
2 ·工法特点
1) 筒仓预埋件环梁处施工工艺加快了施工进度、提高了工程质量,又具有十分良好的节能效果和综合经济效益。2) 本工艺避免了因等待环梁混凝土达到设计强度而造成的人员窝工,改善了工人作业的劳动条件,降低了劳动强度。3) 本工艺将原先环梁整体箍圈分成两部分,第一段浇筑混凝土,另一侧用泡沫板填充做模板,第二段浇筑环梁剩余部分来分段浇筑环梁,控制混凝土内部的水化热,混凝土内部振捣密实,保证混凝土施工质量。4) 本工艺通过滑模操作平台来施工环梁,不需要另外搭设操作平台,降低了施工难度,缩短了施工周期。
3· 适用范围
筒仓预埋件环梁处施工工艺可用于建筑工程中各类壁厚的筒仓、造粒塔等工业建筑,尤其适用于仓壁处设有预埋件的环梁构筑物。相关混凝土承载力、钢筋强度等一系列参数需经设计单位验算并符合规范同意后方可施工。
4· 工艺原理
筒仓预埋件环梁处施工工艺的原理是将原先环梁整体箍圈分成两部分,第一段混凝土浇筑壁厚度为150 mm,另一侧用泡沫板填充做模板,第二段混凝土浇筑为环梁的剩余部分( 见图1) 。
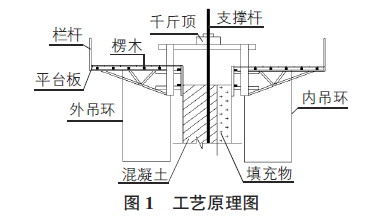
5· 施工工艺流程及操作要点
5. 1 施工工艺流程
支模、绑筋→先浇筑150 mm 壁厚混凝土( 另一侧用泡沫板填充做模板) →滑模系统滑至超出环梁顶400 mm 位置→绑扎环梁第二道箍圈→加设支撑杆( 48 钢架管) →预埋钢筋、钢板→浇筑环梁剩余部分混凝土。
5. 2 操作要点
滑模系统支撑完毕后,自基础环梁上标高开始滑模,滑升到漏斗环梁标高处利用滑模系统浇筑部分混凝土( 漏斗环梁为不规则的牛腿形状) ,剩余部分用竹胶板加钢架管支撑系统进行浇筑。
5. 2. 1 混凝土施工
1) 由于环梁分两次浇筑,为方便施工,经与设计沟通将原先整体箍圈分成两部分,第一段混凝土浇筑厚度为150 mm,第二段混凝土浇筑厚度为150 mm。2) 浇筑150 mm 壁厚混凝土时绑扎第一道箍圈,另一侧用泡沫板填充做模板,浇筑完毕后绑筋,绑扎第二道箍圈同时预埋钢筋和钢板,预埋钢筋和钢板焊接,最后整体浇筑剩余混凝土。3) 浇筑环梁另一侧混凝土时,应将先行浇筑的环梁内壁( 接槎面) 进行凿毛处理,一是将松散混凝土剔除,二是凿毛时最好形成坡口,这样易结合可提高整体强度。具体凿毛的标准按照4 cm × 3 cm 或5 cm × 4 cm( 水平尺寸与深度) 凿坑,四周间距10 cm ~ 15 cm,坑的密度越大,两次浇灌的接触面积也就越大,结合力也就越强。第二次浇灌时可加膨胀剂或采用高一标号的混凝土,混凝土施工图见图2。
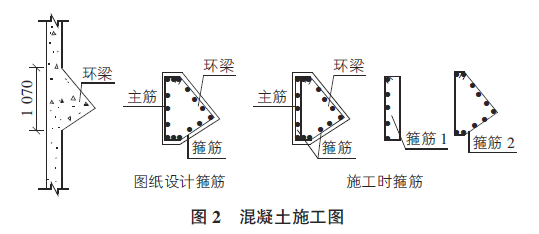
5. 2. 2 支撑系统加固
由于漏斗环梁处先分段浇筑150 mm 厚的筒壁混凝土,所以该处必须对支撑杆加固处理。具体加固方法为: 在原有的滑模系统支撑杆间再加设一根48 钢架管,深入下部混凝土600 mm,深入上部混凝土400 mm,为保证其整体稳定性,水平设两道拉杆,间距为600 mm。支撑杆示意图见图3。
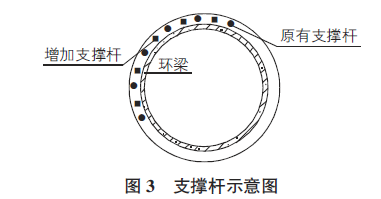
6·机械及设备投入计划
本工艺采用的机械或设备投入计划见表1。
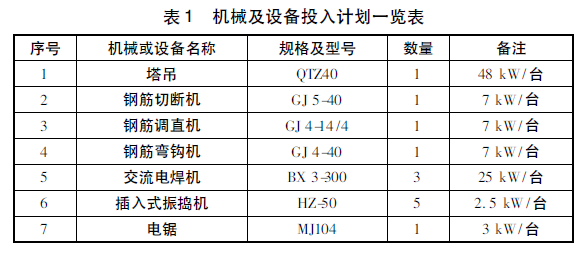
7· 质量控制
1) 工程质量控制措施。本工艺严格遵照施工技术规范和行业施工技术规程等进行施工和质量控制。2) 质量保证措施。预埋件和预留孔洞的施工方法: 采用直埋法,门、窗等洞口的胎模采用木模板和方木制作,宽度应小于滑升模板上口10 mm,并与仓壁钢筋固定牢靠。当达到预埋件埋设标高时,将预埋件与仓壁钢筋焊接,预埋件应与模板有一定间距,避免模板滑升时与模板接触,而产生挂模现象。
8 ·安全保证措施
1) 明确各人员安全生产责任制,认真贯彻执行“安全第一,预防为主”的方针。2) 作业人员严格执行国家相关法律法规,遵守现场安全管理制度。3) 班组进场前,进行入场安全“三级教育”,贯彻并签字。4) 班组作业前,编制有针对性的安全技术交底,向施工人员进行交底,并履行签字手续。5) 在构筑物仓壁边线外的10 m 范围内划为危险区域,此区内不得站人或通行。6) 构筑物出入口搭设高度不低于2. 5 m 的安全防护棚。安全通道棚顶采用不少于两层纵横交错的木板组成。7) 操作平台铺设的木架板必须严密平整、固定可靠并防滑,不得随意挪动。8) 操作平台设钢制防护栏杆,高度不小于1 200 mm,底部设高度大于180 mm 的挡板,栏杆外满挂安全网封闭。9) 操作平台上不用的材料、小型工具应及时清理运至地面。
9· 文明施工措施
1) 施工现场建筑垃圾按照指定地点堆放,做到施工完毕保持工完料尽,及时清理地面上的落地灰料。2) 泡沫板的堆放要整齐有序,做好防火措施,用塑料布进行覆盖,防止碎屑乱飞。3) 现场施工材料应分类堆放整齐并设置标识牌,分片包干到人。4) 尽量减少夜间施工,在施工时要采取减噪降噪的措施,将噪声控制在允许范围内。5) 做好现场防火工作,灭火设施配备齐全,设置专职消防员,定期进行安全隐患排查。6) 施工场地和道路经常洒水湿润,防止扬尘。
10· 结语
筒仓预埋件环梁处施工工艺与当前我国普遍使用的施工方法相比,有它的合理性、先进性及其适用性。采用前者施工工艺明显加快了施工进度、提高了工程质量,又具有十分良好的节能效果和综合经济效益,其效益可以概述为以下几点:
1) 施工操作简便,施工进度加快,施工质量提高,达到了预期的工期目标和质量目标。2) 施工所用工艺改善了作业条件,降低了劳动强度。3) 采用此工艺降低了工程造价,节约了施工成本,带来了良好的社会及经济效益。